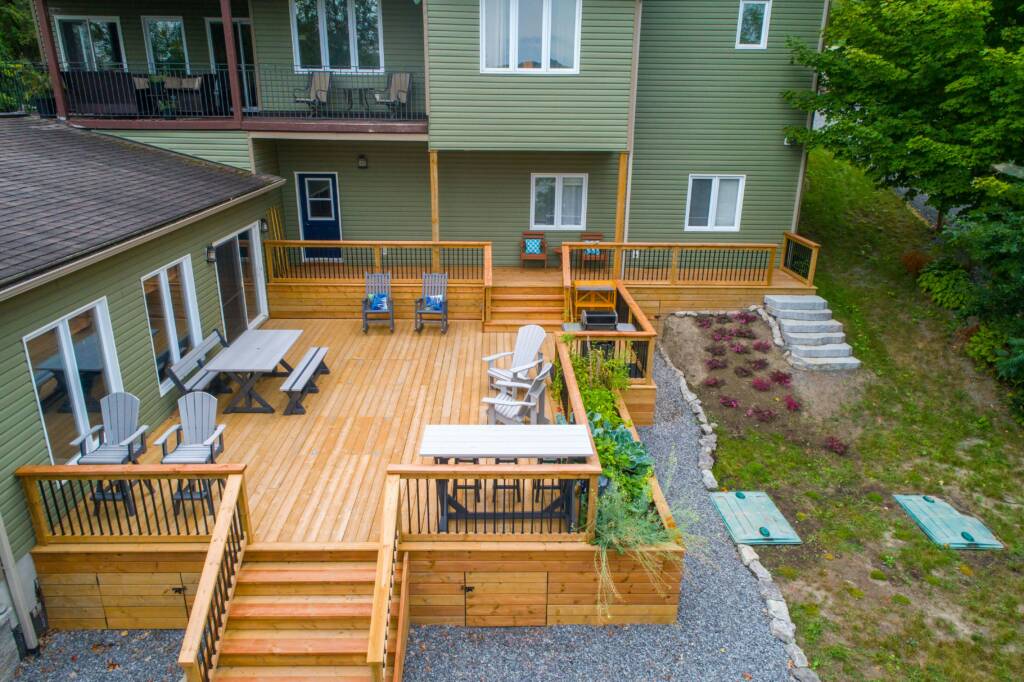
Decks
Building a deck in the Seattle area—or anywhere in the Pacific Northwest—isn’t just about aesthetics. Our region’s wet weather, moss-prone surfaces, and constant moisture exposure can quickly turn a beautiful deck into a high-maintenance headache if not built correctly. Whether you're replacing an old deck or starting fresh, your decisions on materials, design, and contractor selection will have a long-term impact on durability and performance.
After years of inspecting, maintaining, and building decks in this climate, we’ve learned what works—and what doesn’t. This guide covers the best types of materials, how to choose the right contractor, and what common mistakes to avoid.
Choosing the right material is one of the most important steps to building a long-lasting deck:
- Western Red Cedar: A popular natural choice in this region due to its natural resistance to rot and insects. Must be regularly sealed for optimal lifespan.
- Pressure-Treated Lumber: Great for the substructure due to its moisture resistance—but avoid using it as the decking surface (it contains chemicals and can warp).
- Composite Decking: Durable, low-maintenance, and moisture-resistant. Higher upfront cost but long-term savings in maintenance and longevity.
- PVC Decking: Fully synthetic and virtually waterproof. It’s resistant to rot and mildew, making it ideal for shady or damp backyards.
Tip: Avoid untreated softwoods like Douglas Fir or Spruce for decking surfaces—they degrade quickly in our climate.
Best Decking Materials for the Pacific Northwest
How to Choose the Right Contractor
The contractor you hire will determine the quality of the workmanship—and whether your deck holds up to PNW weather.
- Look Local: Choose a contractor with experience building decks specifically in the Pacific Northwest.
- Verify Credentials: Ensure they are licensed, bonded, and insured in Washington State. Check their status on the WA State Department of Labor & Industries website.
- Ask for References: Don’t just rely on online reviews—ask for recent local projects and speak with past clients.
- Compare Quotes Thoughtfully: Get multiple estimates and compare more than just price. Ask detailed questions about materials, hardware, and timelines.
- Review the Contract: Make sure it’s clear, includes all work details, timelines, and payment structure. Avoid contractors who rely on handshake agreements.
From inspection experience, here are the most common (and costly) mistakes homeowners make:
- Waterproof Decks Over Living Space
Trying to make a deck double as a roof is risky. These systems fail over time, and repairs are expensive. Use an under-deck drainage system if you need dry space below. - Overcomplicating the Design
Multi-level decks may look great, but they’re harder to maintain and can limit usable space. A single-level layout is often more practical and durable. - Poor Ventilation and Drainage
Avoid deck designs that trap water or debris (like tight railing bases). Choose railings with minimal contact to prevent rot and allow easy cleaning. - Weak Connections to the House
A poorly attached deck can pull away from the house over time. Upgrade with SDWS ledger screws and tension tie kits from Simpson Strong-Tie for maximum safety. - Inadequate Material Choices
Pressure-treated wood for decking? Skip it. Cheap fasteners? They rust quickly. Use stainless steel or coated deck screws for long-term performance.
Common Mistakes to Avoid
Summary: Building a Deck That Lasts in the PNW
Area | Best Practice |
Material | Cedar, composite, or PVC for surfaces; pressure-treated lumber for framing |
Structure | Prioritize strong footings, ventilation, and drainage |
Design | Avoid tight contact points and overly complex layouts |
Contractor | Hire licensed, local, experienced pros with great communication |
Maintenance | Clean regularly, seal or stain as needed, inspect annually |